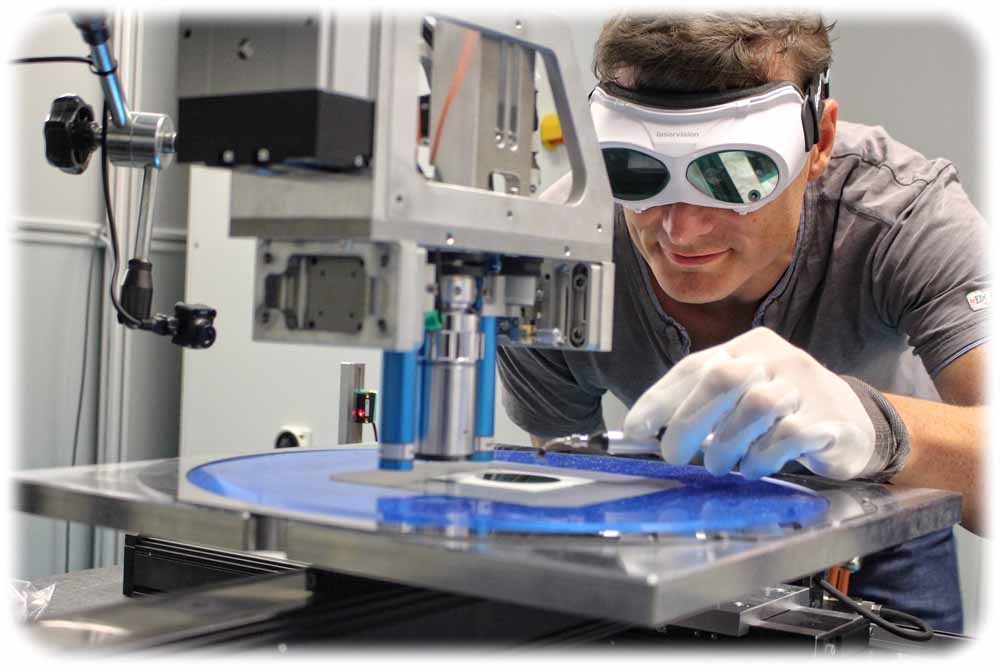
Siltectra-Technik-Chef Dr. Jan Richter positioniert einen Test-Wafer unter dem eigenentwickelten Multi-Photonen-Laser. Foto: Heiko Weckbrodt
Neue Technologie könnte weltweit Millionen Tonnen Halbleiter-Material sparen
Dresden, 24. August 2016. Siltectra Dresden will bis zum Sommer 2018 vier Fabriken bauen, die mit einer innovativen Laser-Polymer-Methode Chipscheiben (Wafer) fast abfallfrei spalten können. Das Halbleiter-Unternehmen rechnet mit Kosten von rund 20 Millionen Euro, die es bei Risikokapitalgebern einsammeln will. Durch diese hochautomatischen Fabriken sollen zunächst etwa 80 bis 100 neue Jobs entstehen. Die Standorte stehen noch nicht fest.
Dresdner hoffen auf Milliarden-Markt für ihre „disruptive Technologie“
„Wir haben hier eine , die die ganze Branche umkrempeln kann“, schätzt Siltectra Chef Dr. Wolfram Drescher ein. „Wir sprechen hier von einem ähnlich revolutionärem Übergang wie damals, als Autos die Pferdefuhrwerke verdrängt haben“, betonte der promovierte Elektrotechniker und Geschäftsführer, der einen Milliardenmarkt für die neuartige Technologie aus Dresden sieht.
Bei Anderen würde man solche Ansagen wohl für die typisch großmäuligen Ansagen vieler Startups halten. Drescher indes hat bereits mehrere Firmen geleitet und zwar recht erfolgreich, darunter die Funkchip-Designschmieden Systemonic und Blue Wonder Communications.
Keine Spanabfall mehr bei Wafer-Produktion
Hintergrund: Um Scheiben („Wafer“) für die Chipproduktion zu gewinnen, ist es heute noch üblich, Halbleiter-Kristalle zu zersägen. Etwa ein Fünftel bis die Hälfte des teuer gezüchteten Materials werden dabei als Späne verplempert. Im Siltectra-Verfahren hingegen gehen nur ein bis fünf Prozent des Materials verloren. Anders ausgedrückt: Während weltweit derzeit noch umgerechnet Hunderte Millionen Wafer als Sägespäne enden, könnte durch die neue Technologie aus Sachsen dieser „Abfall“ im Gegenwert von mehreren Milliarden Euro eingespart werden.
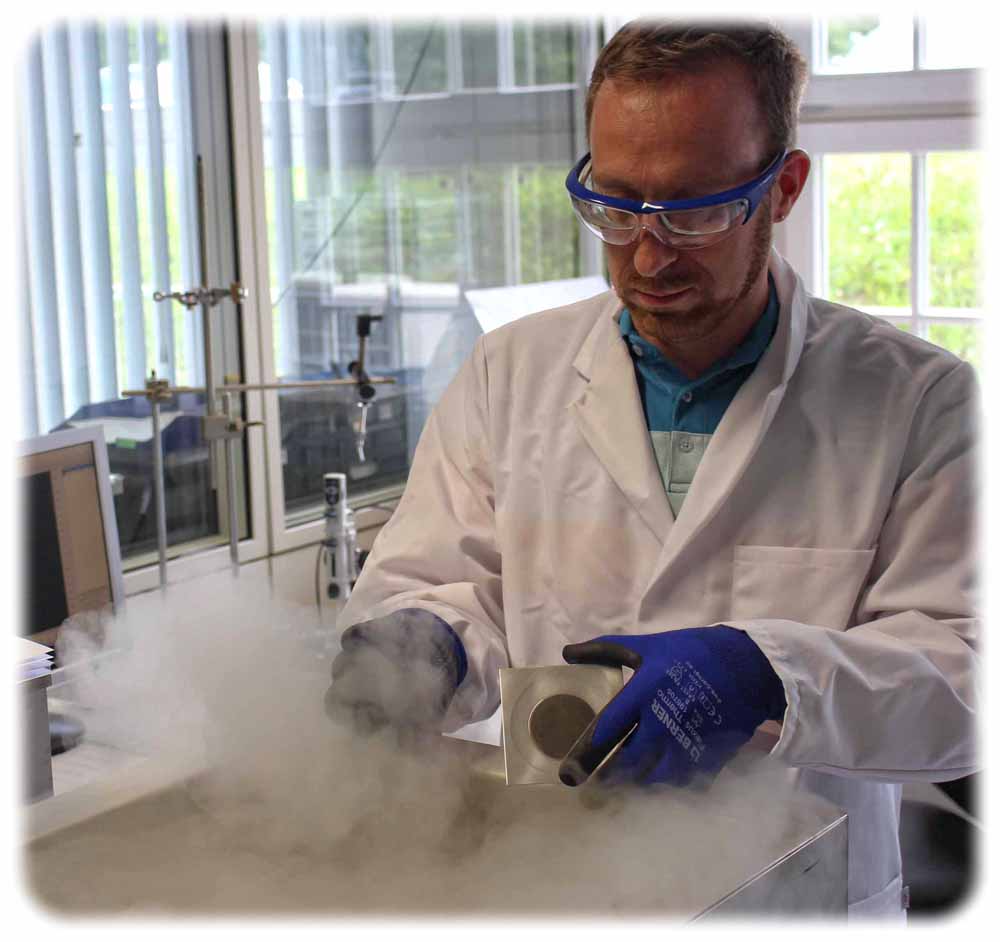
Techniker Gino Gesell spaltet mit flüssigem Stickstoff einen polymer-überzogenen Test-Wafer. Foto: Heiko Weckbrodt
Mulltiphotonen-Laser punktiert Material unter der Oberfläche
Die Dresdner haben dafür ein raffiniertes Alternativverfahren weiterentwickelt, um aus Kristallen Wafer-Scheiben zu gewinnen: Mit einem „Multiphotonen-Laser“ erzeugen sie unter der Oberfläche eine Sollbruchstelle im Kristall. Die besteht für jede Ebene aus Millionen von Mini-Löchern, die nur wenige Mikrometer (Tausendstel Millimeter) groß sind. Dann überziehen sie die Oberseite des Kristalls mit einer blauen Polymer-Schicht. Die Ingenieure kühlen diese Polymer-Qualle mit flüssigem Stickstoff auf sehr tiefe Temperaturen. Durch den thermischen Stress bricht der Kristall an der Soll-Bruchstelle – und ein glatter Wafer entsteht.
Dr. Wolfram Drescher, Geschäftsführer von Siltectra Dresden: „Die Chinesen mögen versuchen uns zu kopieren. Viel Spaß dabei!“
Zeitfrage entscheidend für Markterfolg
Das Verfahren hat neben der Spanfreiheit weitere Vorteile, so können viel dünnere Scheiben als per Säge erzeugt werden. Aber: Anfangs brauchte Siltectra zweieinhalb Tage für jeden Wafer – viel zu lange für den schnellen Takt der Halbleiterindustrie. Zum Vergleich: Die verschwenderische Wafersäge sägt in etwa sechs Minuten eine Silizium-Scheibe mit 300 Millimetern Durchmesser aus einem Silizium-Kristall („Ingot“). „Wir müssen mit unserer Methode unter zehn Minuten pro Wafer kommen“, weiß Drescher.
Von der IP-Company zum Laser-Entwickler
Als Knackpunkt erwiesen sich die Laser. „Anfangs dachten wir, wir finden rasch einen Hersteller, der uns eine schnelle Multiphotonen-Laser Anlage konstruiert“, erzählt der Siltectra-Chef. „Das hat aber nicht geklappt.“ Und bald war auch klar: Wenn sich die Spalttechnologie weltweit in der Elektronikindustrie etablieren soll, müssen die Dresdner schlüsselfertige Komplettanlagen anbieten, nicht nur eine Technologielizenz. „Deshalb haben wir unser Geschäftsmodell überprüft und geändert“, teilte Drescher mit. So begann Siltectra, eine eigene Anlage mit einem 10-Watt-Pulslaser zu entwickeln, die die Spaltzeit pro Wafer auf eine halbe Stunde gesenkt hat. „Mit der nächsten Generation, die mit 200 Watt arbeitet, werden wir unter zehn Minuten kommen“, ist Drescher nun zuversichtlich.
Neues Geschäftsmodell: Siltectra setzt auf eigenes Foundrys
Und letztlich haben sich Geschäftsleitung und Anteilseigner auch entschlossen, dass Siltectra künftig Komplettfabriken (Fabs) einrichten und betreiben wird. Die sollen relativ klein sein (nur etwa 200 Quadratmeter), aber die komplette Anlagentechnik fürs Spalten enthalten. Siltectra will, dass die ersten vier Fabs ab Mitte 2018 als Auftragsfertiger („Foundries“) für die gesamte Industrie agieren.
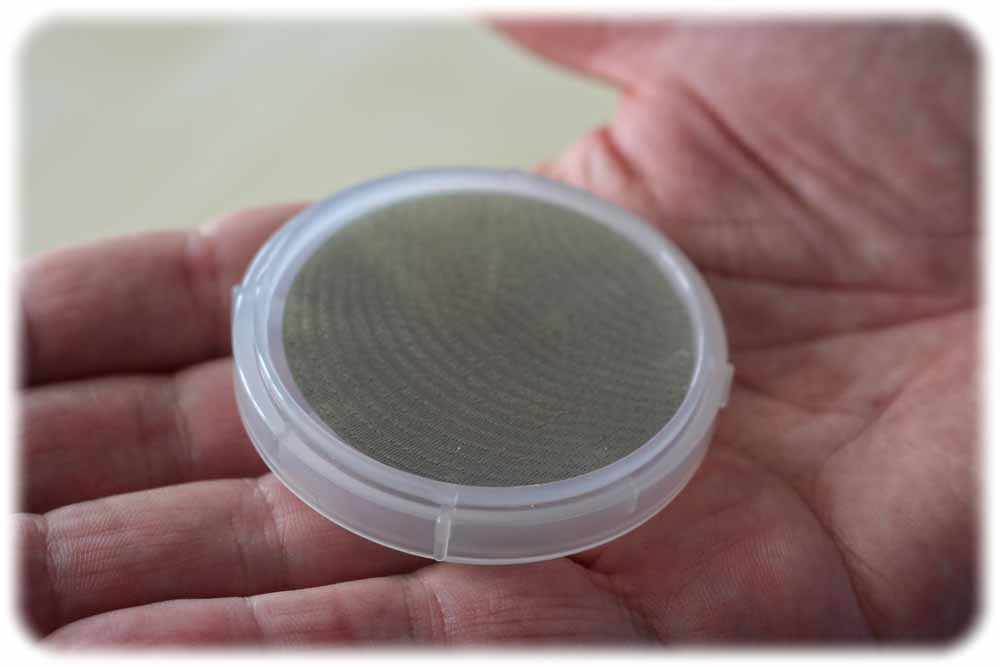
Kosten selbst noch unprozessiert gut und gerne 500 Euro die Scheibe: ein Silizium-Karbid-Wafer, wie er beispielsweise gebraucht wird, um Leistungs-Elektronik für Trafos und Solarkraftwerke herzustellen. Foto: Heiko Weckbrodt
Anfangs vor allem für sehr teure Materialien gedacht
Spezialisieren sollen sich diese Mini-Fabs zunächst darauf, besonders hochwertige Halbleiterkristalle in Scheiben zu spalten: Kristalle aus Silizium-Kohlenstoff-Verbindungen (Siliziumkarbid-Boules) zum Beispiel, die für Hochspannungs- und Starkstrom-Chips in Solar-Kraftwerken oder Trafos gebraucht werden. Bei diesem Halbleitermaterial kostet selbst ein kleiner Standard-Wafer gleich mal 500 Euro und nicht nur 35 wie bei den Silizium-Scheiben. Da lohnt sich eine innovative, noch teure, aber materialsparende Spalttechnologie, wie sie Siltectra am Markt etablieren will.
Dünne Saphier-Gläser für kratzfeste Smartphones
Und auch superharte kratzfeste Saphirgläser für Handy-Bildschirme lassen sich mit der Dresdner Technik in dünne Scheiben zerlegen – Sägen brauchen dafür eine halbe Ewigkeit und bekommen das Saphierglas auch nicht dünn genug geschnitten.
Und wenn das Foundry-Konzept am Weltmarkt ankommt, wollen die Dresdner weitere Auftragsfabriken bauen, womöglich auch in Sachsen. Das Geld dafür möchten sich die Ingenieure – wenn alles gut läuft – über einen Börsengang besorgen, „vielleicht schon 2021 oder 22“, sagt Drescher.
Zahlen und Fakten:
Name: Siltectra GmbH
Sitz: Dresden-Klotzsche
Gründung: 2010
Geschäftsfelder: Wafer-Spalten für Mikroelektronik, Solar- und Bildschirmindustrie
Belegschaft: 13 Mitarbeiter (davon einer in China)
Mehr Infos im Netz: siltectra.com
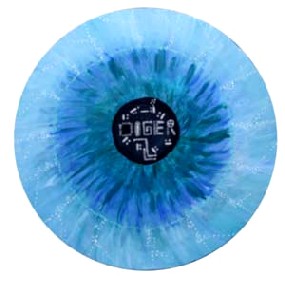
Ihre Unterstützung für Oiger.de!
Ohne hinreichende Finanzierung ist unabhängiger Journalismus nach professionellen Maßstäben nicht dauerhaft möglich. Bitte unterstützen Sie daher unsere Arbeit! Wenn Sie helfen wollen, Oiger.de aufrecht zu erhalten, senden Sie Ihren Beitrag mit dem Betreff „freiwilliges Honorar“ via Paypal an:
Vielen Dank!